In-house
integrated
production
社内一貫生産体制
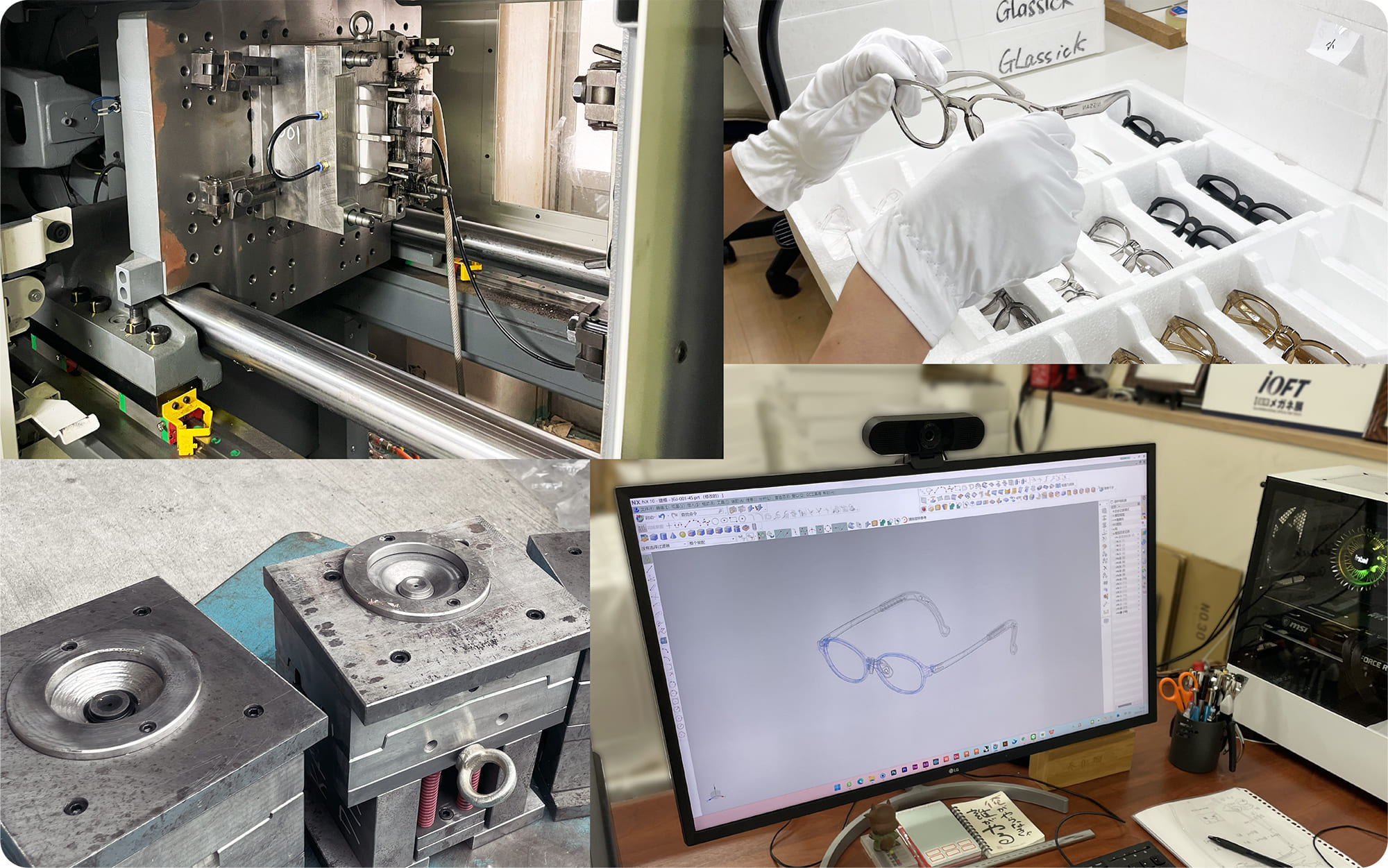
デザインから製品まで。
技術と経験によって作り上げれらる一貫生産体制。
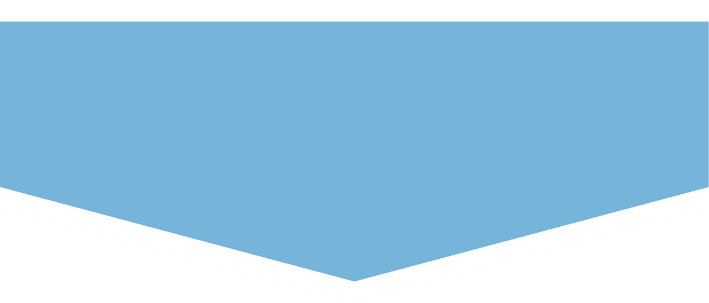
製品企画
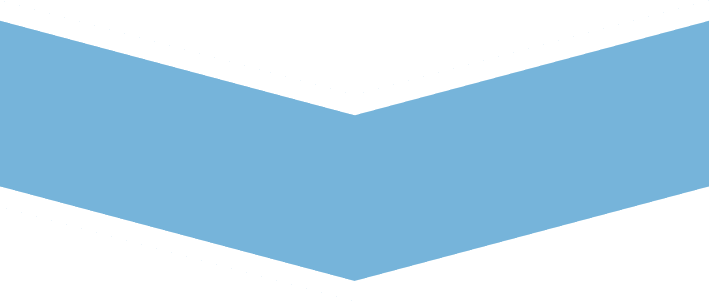
企画開発
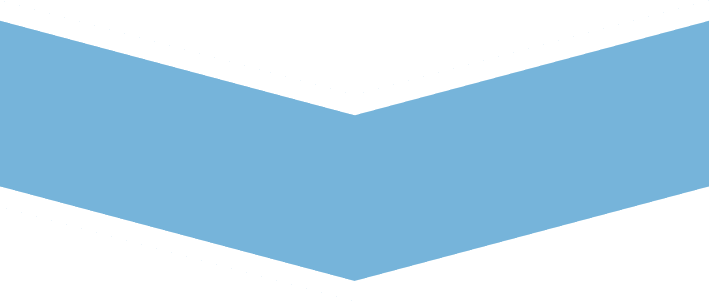
デザイン
平面デザインと3Dモデリングによる、よりイメージしやすいデザイン検討
デザインチームにより、デザイン画や設計図を平面図から三次元データへと変換します。
3Dデータになることでより完成図のイメージがしやすくなるとともに、立体になった際にラインや構造に
破綻がないかの評価を行うことによって、より高い精度でのデザイン確認・修正を行うことができます。
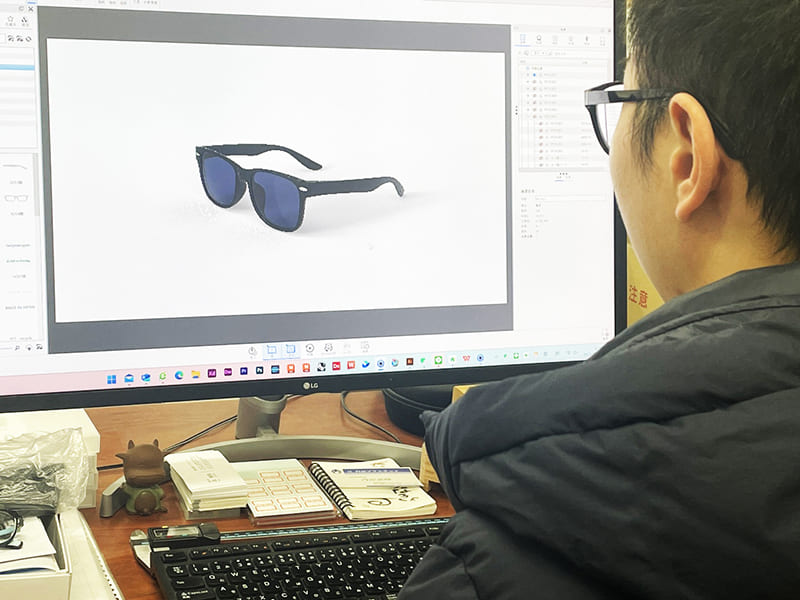
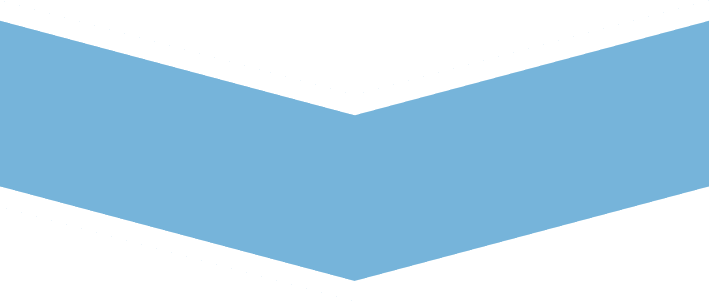
設計精査
3DCADデータを元に、強度面や製造上の問題点などを精査・調整
使用する材質によって強度や製造可能な寸法が異なるため、三次元設計データを用いて
構造や製造工程上での問題点の洗い出しなどの精査を行います。
問題点が見つかった場合には再設計を行い、より完成度の高い製品を目指します。
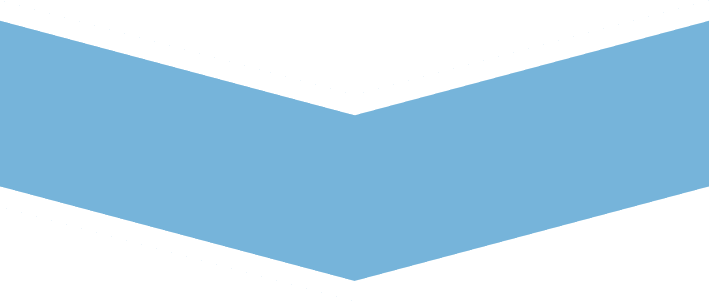
試作評価
3Dプリンタによるモックアップを作成し、デザイン・構造の最終評価を行います。
3Dプリンタで製品と同じ形状の試作モックアップを作成することによって完成品のイメージを固めます。
実際に手に取り、顔に合わせた際のサイズ感などを実物で確認することで、
より完成度の高い製品をつくりあげるための細かな調整が可能です。
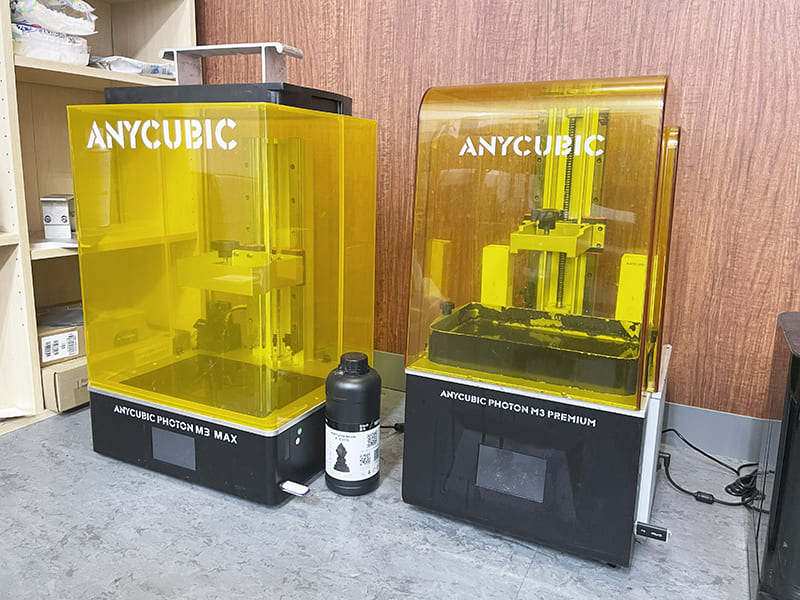
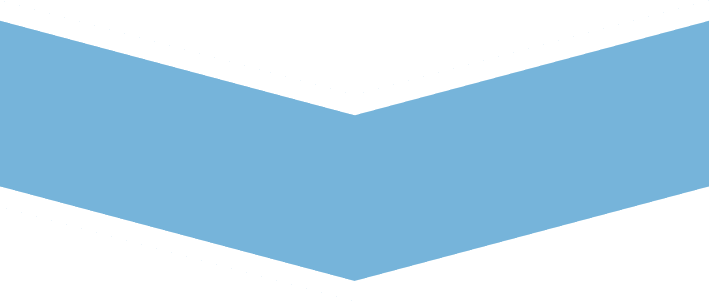
量産製造
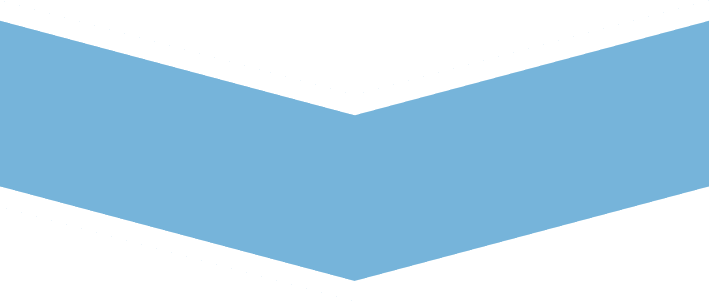
成型加工
品質検査
成型された部品に不良や問題点が無いか1つ1つ検品を行います。
異物や変形などといった単純な目視によって分かる不良だけでなく、 表面の平滑度や部品の箇所ごと強度の違いなども含めて 一つ一つ人の手によって確認・検査を行っています。
表面加飾
独自印刷技術による様々な表現の表面装飾
通常の技術では難しい立体物や曲面に対しての印刷が可能です。
様々な色や質感の表現が可能なフルカラー印刷や、剥離の心配のない含浸印刷などがあります。
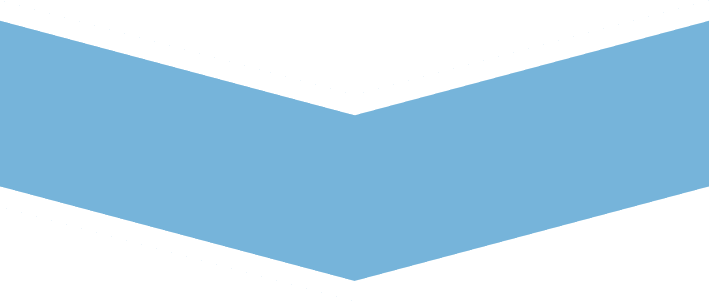
組立調整
製造した部品を組み上げ、出荷可能な形状への調整を行います。
表面処理などを行った最終部品を組み上げます。
レンズのはめ込みや左右の傾きの調整などののちに、クリーニングを行い
商品として出荷可能な状態に仕上げます。
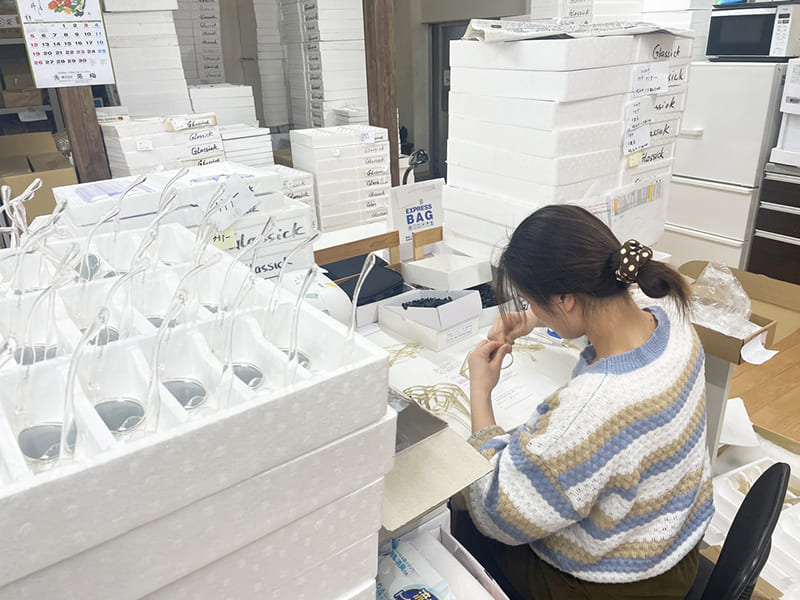
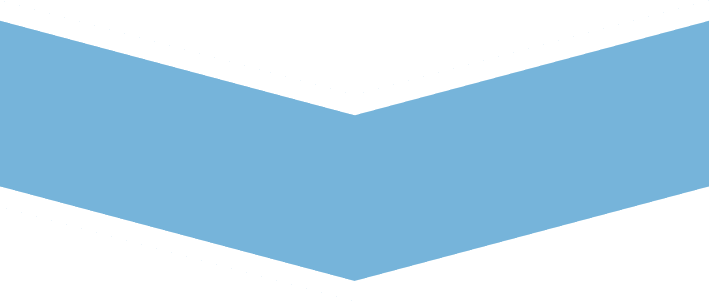
製品出荷
完成品を袋詰め・梱包して出荷します。